Roll Texturing
Roll texturing service represent a process of changing inside structure of the metal material, or surface structure of the material of the workpiece (work roll from finishing Rolling Mill lines) by controlled electrical discharges where electrical pulses were generated between an electrode and a work roll, which results in the formation of micronic craters and recesses on its surface.
Process
By this process it is created an adequate material structure of the roll resulting in increased quality of the final cold rolled products and specifically: quality uniform over the entire surface of steel (as well as AL) cold rolling sheets, better absorption of color at painting especially car bodies (better painted appearance), possibility of applying a wide range of finishing treatments of the shits, etc. The quality of the roll surface, that can be reached by this process is within the average roughness Ra = 1–10 µm and 240 to 25 Pc / cm (Picks per cm area).
This treatment allows a higher number of micron-formed craters/peaks on the roll surface, then a higher repeatability of the process and a wider range of roughness achieved. Cold rolled steel sheets for the automotive industry and other related steel products obtained by pressing (plastic deformation of the sheet), are basically all manufactured by the work rolls with the changed texture of the material surface.
There are two main reasons for texturing the work rolls:
- Increasing the level of forming (deformability) cold-rolled steel sheets, due to the fact there are in the micro craters and recesses on the surface of a metal sheet that are transferred from the work rolls during the rolling process, rolling oil retains and allows constant lubrication of contact surfaces of the drawing press and sheet steel during the process of several stages of the forming respectively deep drawing (pressing).
- Improving the adhesion of paint and finishing process of the painting cold rolled steel sheets with such texture, which is one of the main demands of the automotive industry.
Texturing process is based on the erosion of metal surfaces of work rolls in their processing, under the influence of an electric arc / spark which is formed between the electrode (respectively Anode, which is usually dipped in a dielectric oil) and the workpiece / roll which are textured (in this case the work roll is Cathode).

- Electrode (copper)
- Electric power pulse / Ionized (conductive) channel of forming the sparks
- Non-conductive (dielectric) Oil
- Work piece / work roll from Cold Rolling Mill stand
As the texturing machine during operation creates a micronic craters by the mean of controlled electrical discharges, then in such working environment with dielectric it comes to forming of an electric discharge between the electrode and the work roll, wherein the electrical pulse in the form of the sparks drains away eroded particles from the surface of the work roll.

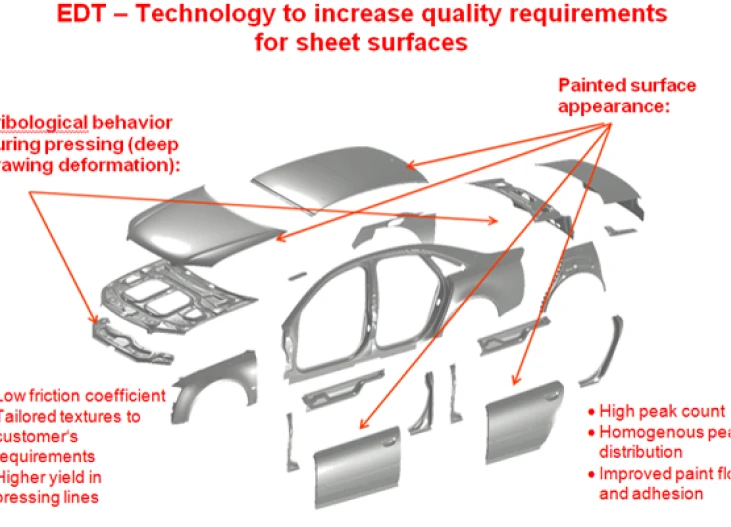

Technology
Generally, nowadays in the world applies four basic techniques of so-called Texturing respectively metal surface texture changes, or precisely steel work rolls:
1. SBT / Shot Blasting Texturing – work roll rotates around its axis and is set in a closed chamber where it is exposed bombing of steel balls (so called buckshot) under the influence of centrifugal rotation wheel, thus causing plastic deformation of the surface structure of the work rolls barrel. Roughness is achieved in the range of Ra=1,5–6,0 micron and can be controlled by the rotational speed of the centrifugal wheel or by the rotational speed of the roll itself, in which however the quality of this method largely depends on the hardness of the roll.
2. EDT / Electro Discharge Texturing – in this method so-called Changes of Textures by Electrical Discharges, work roll rotates around its axis and is set in a tank with a dielectric oil which is on one side or both longitudinal sides of the roll placed a set of electrodes through which the electrical energy with adequate strength are passed and becomes exposed to an influence of the electric pulses in the form of sparks that erode the surface of the roll by forming micron-craters which are characterized by the shape and height of the peaks respectively the peaks and recesses of the crater. Compared with the method of Shot Blasting metal, EDT method enables the achievement a higher number of peaks as well as the frequency of process repetition and a wide range of surface roughness (Ra = 0–15 microns).
3. LT / Laser Texturing – laser beam is directed by the focus on the work roll barrel, whereby a helical rotary wheel by its turning and positioning of the blades interrupts the beam so that the laser operates intermittently and on that way in a controlled environment melts a point of impact on the roll surface by creating the appropriate craters with peaks and recesses. Metal that are melted under the influence of the laser is drained by the plasma and under the influence of inert gas (O2, CO2, Ar). This technology enables the control arrangement of the craters as well as various combinations of peaks size and the shape of the recesses, which obtains controlled different combinations of roughness values.
4. EBT / Electron Beam Texturing – this method uses a very powerful beam of electrons that are in a vacuum environment through the corresponding lens act on a work roll that rotates around its axis and gradually move forward, thus creating micron-craters with a metal rim. The process can be repeated indefinitely with extremely high precision, whereby this method enables creating both type of textures – deterministic and pseudo-stochastic texture.
5. ECD / Electro Chemical Deposition – this method patented by a German-Swiss company TOPOCROM actually is based on a classical electrochemical process of applying hard chrome plating respectively hard chrome plating, with the difference that here the parameters of chrome plating process are controlled by a computer by its combining obtains the required roughness and the corresponding number of peaks. With this method it is possible to achieve a roughness in the range Ra = 0,5 – 12 microns or number of peaks Pc = 100 l/cm.

Methods like SBT, EDT and ECD belong to the group of “stochastic” methods respectively they provides irregular shape of micron craters on the work roll barrel, while methods like LT and EBT belong to the group of “deterministic” methods which obtains regular and proper shape of the subject micron craters.
In fact, of all the above methods only EDT, EBT and LT methods represent a significant improvement now already obsolete SBT method, from the standpoint of roughness stability, the quality of texture undulating, then by high level of forming in deep drawing presses, as well as the color appearance applied to the cold-rolled steel sheet which is mandatory treated by the textured work rolls used in order to manufacture steel strip for car body forming.

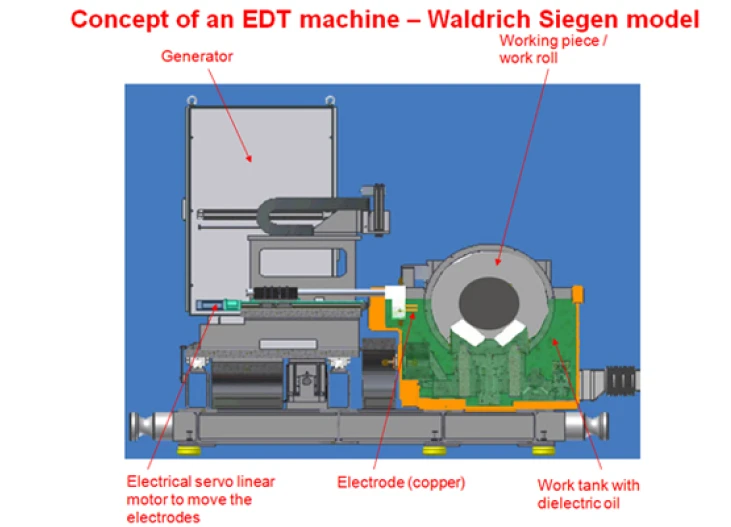
Technical Characteristics
Since the Roll texturing treatment of texturing rolls actually is a process in which under the effect of controlled electrical pulses between the electrodes (one, two or more rows of them) and the roll itself are forming micron craters and peaks on the roll surface, whereby the process can be carried out in a solution of a dielectric fluid depending upon the design of an EDT machine.
Nowadays in the world are widespread two types of EDT machine designes, classified by manufacturers who produce them:
1. SARCLAD / Herkules model of EDT machines: working principle is that the work roll rotates around its axis and realizes movement ahead only by the entire length of roll barrel, passing so aside to the one or two working heads for texturing within which are created micron craters and represses by the means of the corresponding electrodes (can be made of graphite, copper or so) and dielectric oil respectively there are changing the surface texture of the roll itself.
Technical characteristics of the SARCLAD EDT machine follows: operating mode pulse (+), e.g. 36 electrodes made from graphite distributed on one texturing head (for the production of up to 400 work rolls per month), the required amount of dielectric oil in the tank of the texturing heads about 2,500 liters, the range of achievable roughness Ra = 0,5–13 microns.

2. WALDRICH Siegen model of EDT machine: working principle is that the work roll is immersed in the tank with dielectric oil, whereby it rotates around its own axis and makes an oscillatory movement back and forth in the appropriate step, where on one side or both sides are directed copper electrodes that by means of the generator and the electrical impulses produced creates micron craters and valleys on the surface of the work roll.
Technical characteristics of the WS EDT machine follows: operating mode pulse (+ / -), eg 20 electrodes from copper arranged on one side of the work roll in the tank with a dielectric oil (for production of up to 400 work rolls per month), the required amount of dielectric fluid in the tank approximately 14.000 liters, the range of achievable roughness Ra = 1,0 – 15 microns.
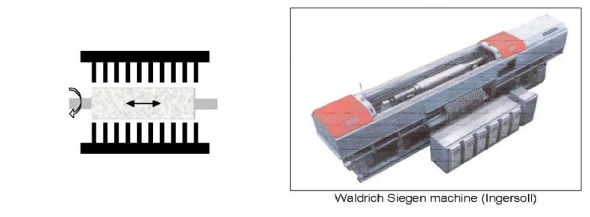
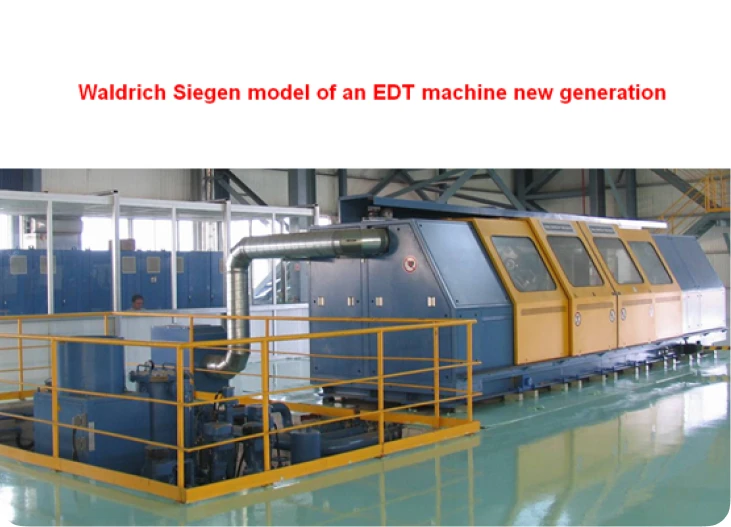
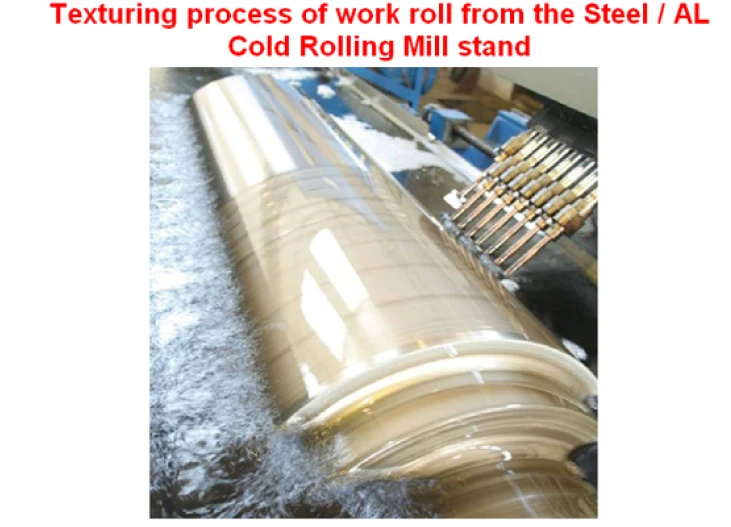